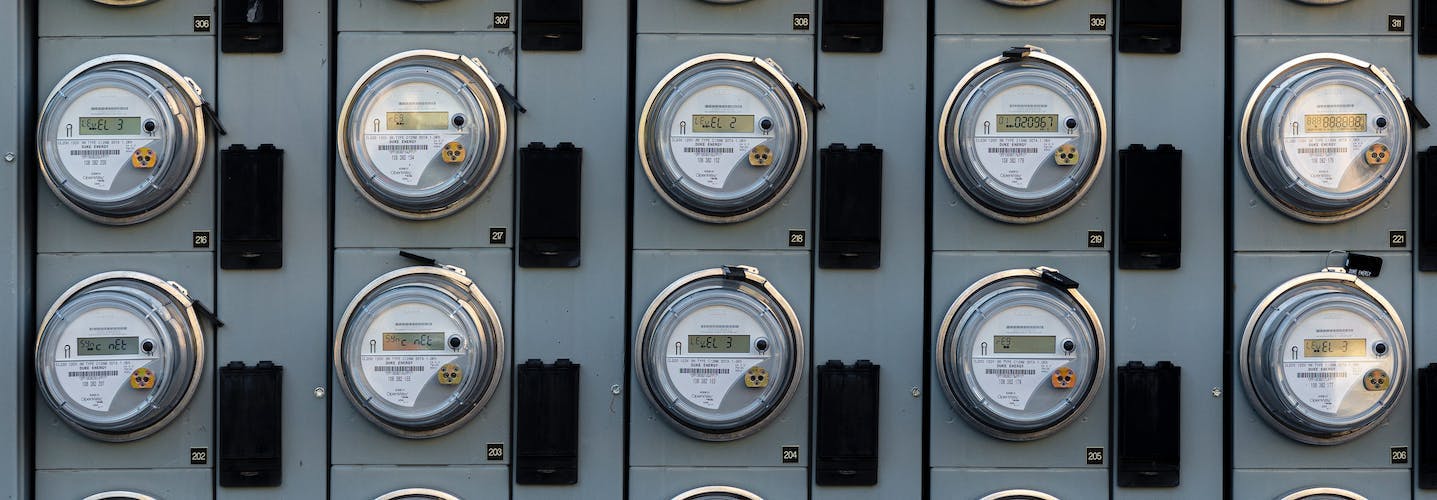
Energy efficient indoor farming
The energy footprint of vertical farms raises concerns about their environmental impact and economic viability, especially with rising electricity prices. At Orius, we're committed to building energy-efficient systems and continually updating them with the latest technology. We're also creating solutions to reduce energy usage in controlled-environment crop production. In this article, we'll share current figures and our roadmap for a more efficient future.
Where we currently stand
One BiomeboxⓇ of 10 m² cultivated area on 4 layers consumes around 23 kWh of electricity per day, i.e. ~7500 kWh per year at a utilization rate of 90% (11 months p.a.) in the standard conditions of 250 µmol/s/m² PPFD, 16 h/day photoperiod, 20°C temperature and 70% relative humidity.
The figures below are provided for this specific application. Indeed, yield and growth conditions differ from one application to another ; a higher PPFD would drive up consumption, whereas a higher target temperature and humidity would generally decrease it.
In those assumed conditions, the BiomeboxⓇ’s daily consumption breaks down as follows :
- 60% = 14 kWh/day consumed by lighting
- 30% = 7 kWh/day consumed by the HVAC system
- 10% = 2 kWh/day consumed by irrigation pumps and water treatment, fertigation & automation equipment
It adds up to a total of ca. 700 kWh of electricity per full month, for a budget between 50 to 150€ per month (depending on the contract)
Our recipe for efficiency
As the breakdown shows, ensuring the lowest energy consumption mainly relies on using top-efficiency lighting and HVAC systems.

First, we take great care in selecting LED systems. It means using the best chips available and fixtures with a good thermal design, to produce as many usable photons as possible per kWh of electricity and limit waste heat. LED lights should not just be energy-efficient, but also have a long lifespan, ensuring a limited Total Cost of Ownership and environmental impact in the long run. Choosing value-engineered fixtures for their low upfront cost is a bad idea, as they rapidly cost-spiral in operation due to poor efficacy & photon output degradation over time. Indeed, during its lifetime, around 80% of the total cost of an LED light comes from the electricity it consumes. The capability to dynamically adjust the spectrum gives a leverage for the producer to further optimize electricity consumption by using custom lighting profiles to match the crop’s needs. Additionally, for high PPFDs (> 800 µmol/s/m²) we opt for water-cooled fixtures to remove heat loss from the grow environment directly at the source, avoid microclimates, and save energy on maintaining temperature and humidity.
On the HVAC side, our current systems use multi-pipe heat pumps that simultaneously generate cold and hot water with a high efficiency (TER 8). This drives the cooling & dehumidification process in each BiomeboxⓇ or grow room for our larger-scale installations. We can thus maintain a fully closed environment for a reasonable cost. The benefits include the most stable climate control, full water and CO2 recirculation, as well as enabling live CO2 uptake & ETP measurement, and easy pressure control of the grow unit if required.
Other equipment, such as pumps and automation devices, use little electricity in comparison, but we are always implementing solutions to make them more efficient. For example, all irrigation & circulating pumps are equipped with variable frequency drives to optimize power consumption depending on the demand in water flow. As the grow facility gets bigger, the electric consumption of those auxiliary devices tends to take a smaller share of the total, but economies of scale have little effect on lighting and HVAC energy footprint.
Perspectives for short-term improvements
LED semiconductors are constantly progressing and chipmakers are expected to improve energy consumption of their components by ~3% per year through technical upgrades, potentially hitting a physical barrier at some point in the future (the maximum photoelectric efficacy is expected to be around 4,2 µmol/J). This still leaves, with the existing technology, at least 25% potential savings compared to now. Also, energy savings made on lighting come with an additional gain, as they directly contribute to reducing heat loads in the environment and thus demand in power from the HVAC system.
Relying on the external environment to harvest free light and heat is also a solution to further decrease reliance on electricity, though this will often be an opportunistic take, depending on project location and crop parameters. For example, HVAC can easily be fitted with free-cooling to save up to 30% overall energy consumption depending on project localization : in northernmost places, our indoor farming facilities could virtually be climate-controlled for free, by harvesting frigories in the outside air.
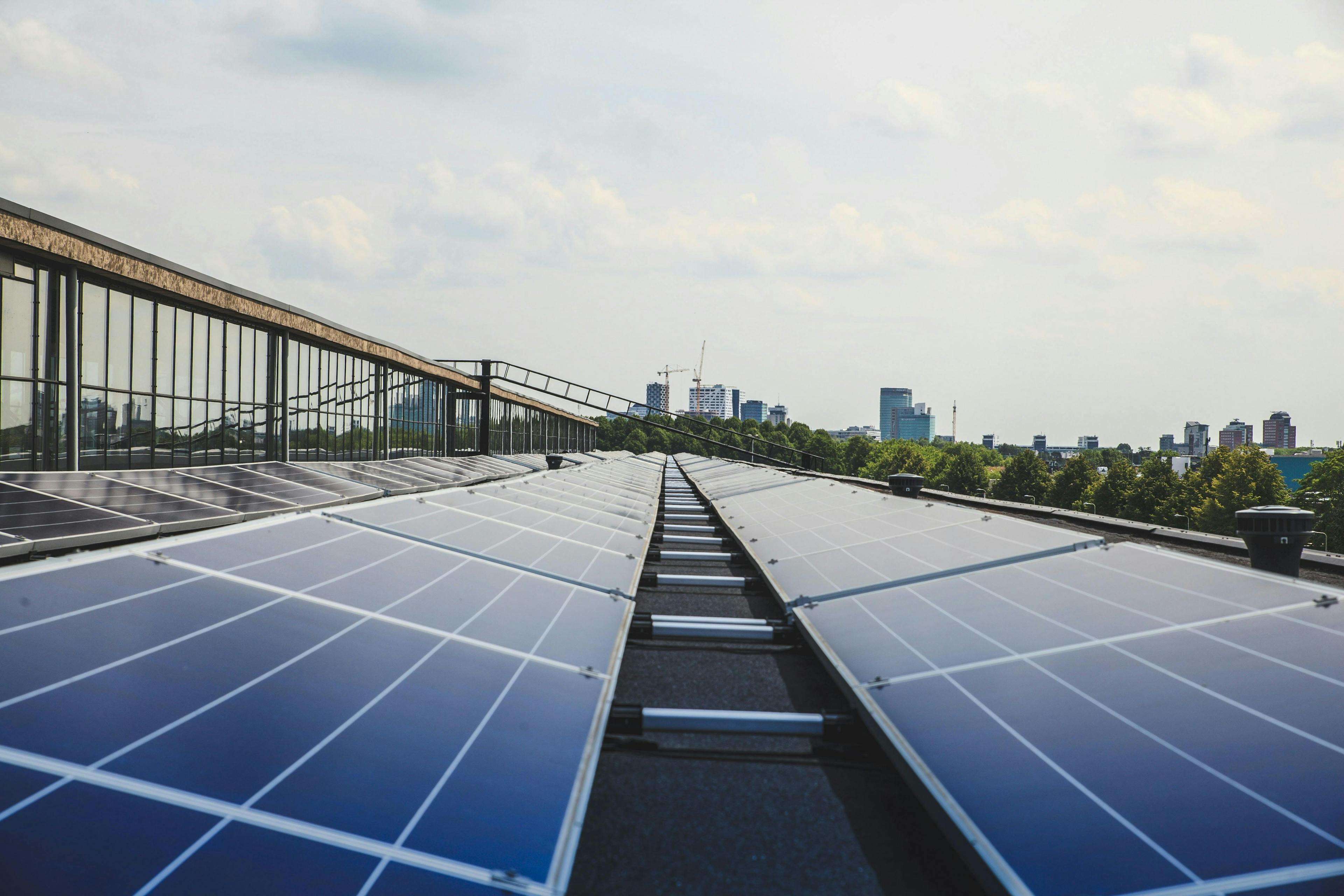
Optic fibers have already been thought of as a way to bring free light into the environment, but the solution is not yet mature industrially. It brings in additional challenges regarding infrared and UV light, on top of its high investment cost compared to photovoltaics. The latter is already a solution: at French latitudes, 18 solar panels (total area 36 m²) could generate each year the amount of electricity required to power one 10-m² BiomeboxⓇ, for a budget around 10 k€. Payback would be achieved between 5~15 years, depending on the evolution of electricity prices. This is especially relevant if the grow facility is set up in a dedicated building whose roof can be equipped with a PV installation.
Other possible synergies could include valuing waste electricity, cool/heat and CO2 from a nearby industrial plant. Nevertheless, greenhouse growers will most benefit from those opportunities as low-temperature heat is generally the only fatal energy source that is not already valued, whereas indoor farming installations mostly need light and cooling. On the contrary, valuing green waste of indoor facilities in the form of biogas has a poor chance to offset energy usage significantly, as its contribution would be negligible.
Indeed, biological processes like photosynthesis curb energy efficiency of indoor cultivation: for most crops, only 1~5% of the energy received by a plant in the form of light is transformed into organic mass. Out of it, only a fraction of that matter is edible or can be utilized. Which means the potential for improvement remains vast. However, biomass conversion efficiency is limited by genetics and cannot just be engineered easily.
Our strategy for making indoor production more energy-efficient
We would rather not bet on hypothetical future technological leaps, or local opportunities, to reduce power demand per kg of biomass produced. We are committed to leveraging Controlled Environment Agriculture technologies to drastically increase the quantity of nutrients and chemical compounds produced in plants and other organisms. This development of high-value ingredients' production systems for industrial-scale applications that use the minimum amount of inputs and energy is how we make indoor production energy-efficient.
Investing all one’s efforts into improving hardware efficiency is not sufficient, as physical barriers put a hard limit : as long as we cannot leverage the production of light, getting one joule of photons will always require more than one joule of electricity. On the contrary, if we can drastically increase the amount of useful matter obtained with a given quantity of time, space and inputs, we can allow highly efficient production processes that require fewer materials and electricity for the same outcome. This is why we are focusing on solutions to drive up net yield, that will consequently make concerns about energy less substantial eventually.
To make it possible, we rely on the unparalleled ability of our growing systems to steer the crop and offer new paradigms in environment control. We also provide researchers and growers with ways to monitor precisely what’s really happening in the plant – not just at the environment level (e.g., by measuring temperature, humidity and CO2 like on most current approaches). Limiting observations to the environmental level gives only a shallow vision on how to play with biotic and abiotic factors and improve those biological processes to drive up the yield.
We think total-environment-control approaches are most capable of drastically driving up production efficiency and the level of quality in producing complex compounds. Open hydroponics systems may be relevant to produce quality produce at a large scale, but ultimately lack the level of control and stability required to develop advanced applications. Stay tuned, and you will witness how we are actually transforming this vision into real-life business cases.